Automotive Industry Castings
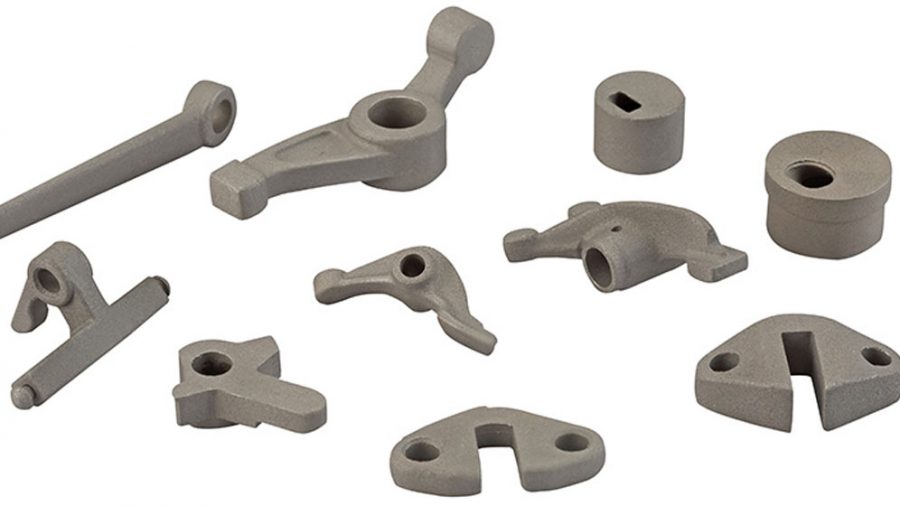
When it comes to manufacturing innovation, the automotive industry is at the forefront of the technological world. With each passing year, carmakers improve their design and engineering systems to create more efficient and powerful vehicles. Alloys and metal casting are often at the heart of these advances, reducing the overall weight of a car while maintaining its overall strength.
One of the most popular casting processes in the automotive industry is sand casting. This process uses moulds and various alloys to produce a wide range of automotive parts. Sand casting is ideal for small to medium part runs because the mould breaks at the end of the cycle and is easy to build quickly.
12.07.2025
Related Posts